Necelých sedm kilometrů od Prostějova, v Kralicích na Hané, sídlí společnost Linaplast, která patří k předním českým zpracovatelům plastů. Její moderní výrobní závod vyprodukuje ročně až třicet milionů výrobků – zejména plastových dílů pro automobilový průmysl.
Firma Linaplast, jejíž počátky sahají až do počátku devadesátých let, byla založena v roce 1997 a doposud setrvává v českých rukou. Nemění se ani její hlavní výrobní program, zaměřený na zhotovování výlisků, přípravků i jednotlivých forem pro vstřikování plastických hmot a pryže.
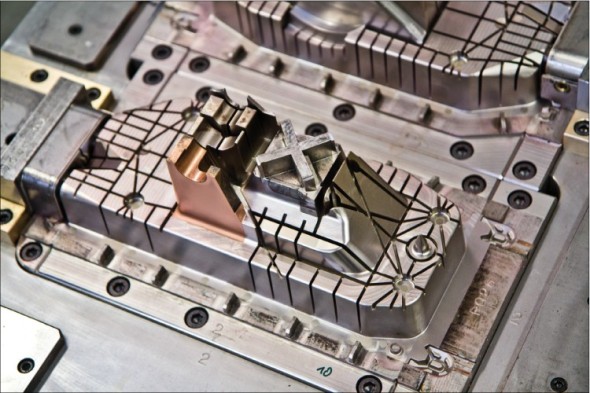
Konkurenční výhodu staví podnik na tom, že klientovi dokáže poskytnout vše potřebné k úspěšnému převedení nápadu do fáze kvalitního výrobku. Odborníci v Linaplastu umějí poradit při řešení designu i funkčních požadavků a zajistí vše od vývoje prototypu po sériovou výrobu, pokud si ji zákazník žádá.
Spolehlivá příprava výroby
Technolog Petr Samson oceňuje, že majitel firmy vnímá potřebu využívat ty nejlepší nástroje, které trh nabízí. Pracoviště, na kterém působí, se nachází v těsném sousedství nástrojárny. On a jeho kolegové na svých počítačích připravují výrobu vstřikolisových forem. Využívají k tomu CAM systém PowerMill od společnosti Delcam s moduly pro tříosé a pětiosé souvislé obrábění. Sám Petr Samson přišel do Linaplastu před několika lety z firmy, která využívala CAM systém jiné značky. Naučit se ovládat produktivně PowerMill mu netrvalo déle než čtyři týdny a nyní na něj nedá dopustit: „Víceosé programování je v systému PowerMill mnohem jednodušší, člověk se s tím nemusí nijak trápit,“ říká a dodává, že když se ho pokoušela přetáhnout do svojí výroby konkurenční společnost, jedním z důvodů, proč nabídku odmítl, byl právě fakt, že dané pracoviště nebylo vybaveno řešením od Delcamu.
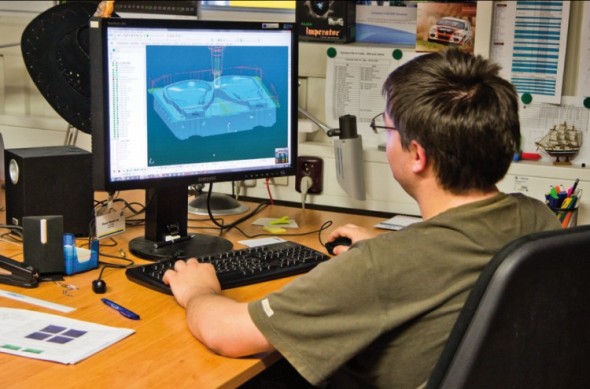
Software PowerMill podporuje vše potřebné pro přípravu výroby forem, takže není nutno využívat další aplikace. Díky vestavěné spolehlivé kontrole obráběcího procesu má programátor jistotu, že při výrobě dílu nedojde ke kolizi, což při pětiosém obrábění představuje nemalé riziko s drahými následky. Přesnost simulace zajišťuje mimo jiné využití detailního virtuálního modelu používaného stroje ve zcela stejné specifikaci, jako je ten na dílně.
Pokud pracovník narazí na problém, může se kdykoliv obrátit na technickou podporu od firmy Delcam Brno, jejíž specialisté dokážou poradit nejen s nastavením softwaru, ale řeší také konkrétní úlohy obrábění, při nichž mohou zákazníkovi připravit několik variantních scénářů výroby, jež pak on aplikuje v souladu s vlastními technologickými pravidly podle svých potřeb.
Placená technická podpora firmě vedle tohoto servisu zajišťuje také přísun nových verzí softwaru a pokrokovějších obráběcích strategií, jež jsou účinnější a rychlejší. Zejména rychlost je při vytížení výrobních kapacit firmy Linaplast klíčovým kritériem a podle Petra Samsona lze pouhou změnou obráběcí strategie zkrátit výrobní čas stroje až o šest hodin na jednom dílu.
Čtyřikrát rychlejší hrubování
V Linaplastu začali jako v jedné z prvních českých firem používat například vysokorychlostní obráběcí strategii Vortex. „Na konkrétním tvarovém dílu jsme dokázali díky Vortexu zkrátit hrubování ze čtyř hodin na jedinou hodinu – to je hmatatelná finanční úspora, ale pro nás je to zejména úspora časová, protože naše termíny bývají dosti šibeniční,“ říká Petr Samson.
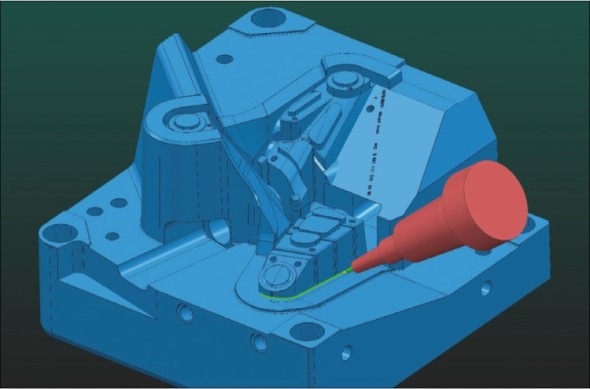
Pro bližší představu, oddělení technologie nyní zvládá v pětičlenném osazenstvu připravit do výroby kolem dvaceti forem ročně. Ty největší váží až jeden a půl tuny a vytvářejí v každém cyklu současně několik výrobků. Data, ze kterých technologické oddělení vychází, pocházejí z poměrně pestré směsice softwaru. Jako dodavatelé v řetězci automobilového průmyslu musí být v Linaplastu schopni zpracovávat data ze systému Catia. Vlastní konstrukční oddělení navrhuje formy v softwaru Pro/Engineer a elektrody v SolidWorksu. Analýza výrobního procesu pak probíhá v simulačním softwaru Moldflow.
Přenos dat do CAM systému PowerMill zajišťuje překladač přímo od Delcamu a technologové se shodují, že jim takové řešení naprosto vyhovuje. Potíže obvykle nejsou ani v případě, že data přicházejí z externích zdrojů v cizích datových formátech. Jakékoliv úpravy geometrie totiž dokážou v Linaplastu provádět velmi flexibilně v softwaru PowerShape.
Vizuální simulace přímo na dílně
Používání aplikací od Delcamu firmě umožnilo zefektivnit i komunikaci směrem na dílnu. Operátoři dostávají do ruky nejen výkres, ale také programový list, takže získávají jasnou představu o tom, jaké budou používat nástroje a nastavení. Pokrokové vedení společnosti Linaplast chce jít ale ještě dál a souběžně s připravovaným pořízením druhého velkého obráběcího centra plánuje instalovat přímo na dílně počítač vybavený prohlížečem dat ze systému PowerMill, na kterém bude možné zkontrolovat také simulaci obrábění a další detaily.
Technolog Petr Samson shrnuje, že díky zavedenému softwarovému řešení od Delcamu jsou on a jeho tým navzdory časovému tlaku schopni produkovat bezchybné podklady pro obrábění. Zvlášť ještě zdůrazňuje aplikaci PowerShape, která jim umožňuje pohotově podle aktuální potřeby upravit geometrii přímo na oddělení technologie, aniž by bylo nutno toto řešit s konstruktéry nebo se zákazníkem. „U Delcamu se dá věřit tomu, co z toho vypadne,“ říká a potěžkává přitom v ruce velmi složitý plastový díl do jednoho z osobních vozů koncernu Volkswagen, který patří k největším zákazníkům Linaplastu.
Připravil Jan Homola ve spolupráci se společností Delcam Brno.